Warehouse Processes & How to Improve Them
Discover everything you need to know about essential warehouse processes, learn how to refine them, and discover how partnering with Tap'in can elevate your order fulfilment.
Eight key processes comprise the warehouse workflow, all of which play an important role in a company’s operational efficiency and order fulfilment success rate. Without a solid understanding of warehouse management best practices across these core processes, it can be hard to maximise warehouse productivity and deliver the best possible experience for your customers.
Here we’ll share our top tips on warehouse process improvement, forged by our years of hands-on experience.
8 Warehouse Processes and Ways to Improve Them
1. Receiving
Receiving is the pivotal first step in your warehouse workflow, setting the tone for everything that follows. While it may seem straightforward, the intricacies of an effective receiving process are critical to ensuring operational success throughout the warehouse.
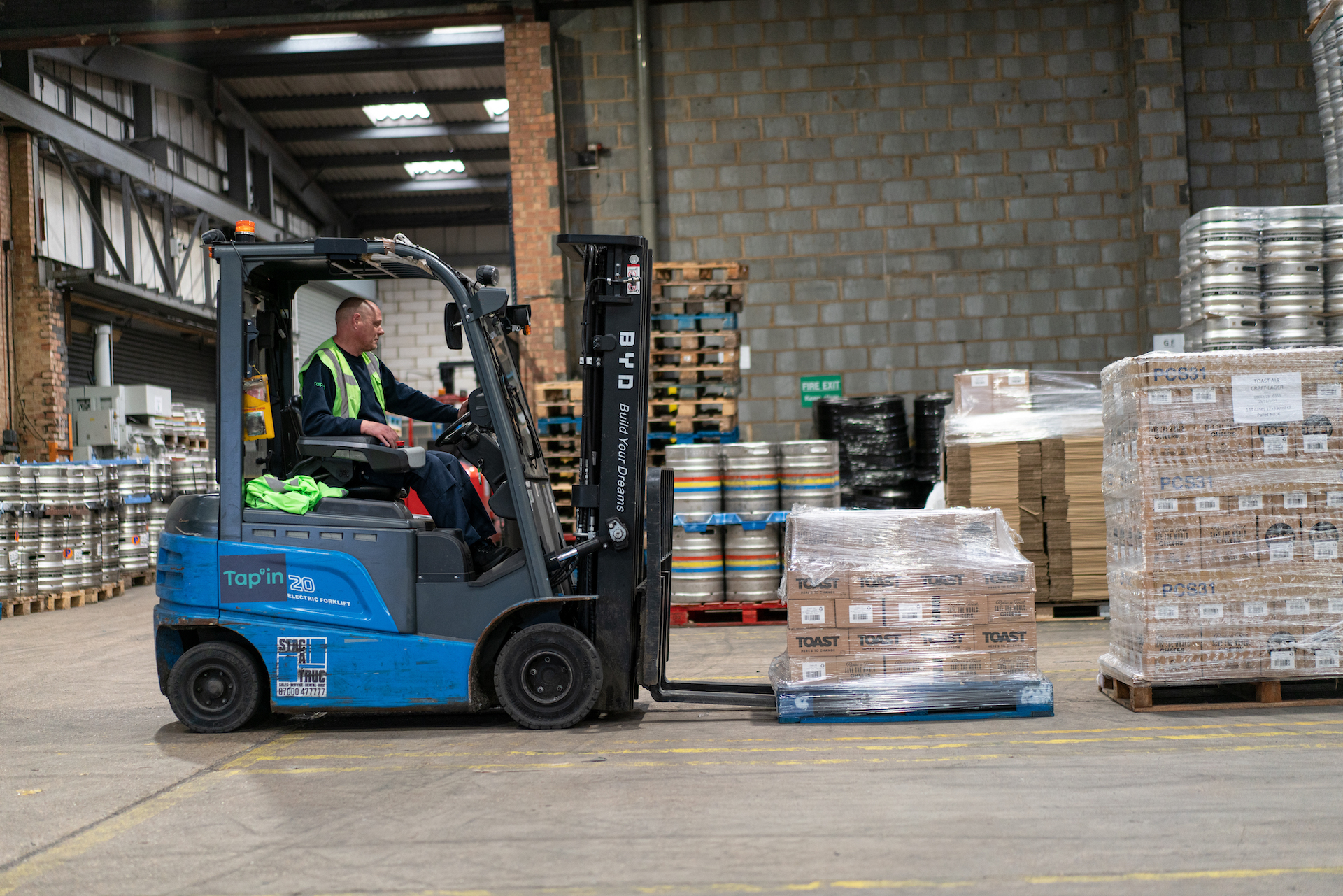
Once products enter your warehouse, the receiving team takes on full responsibility for them. This includes verifying that the correct items, quantities, and conditions align with expectations. An accurate and efficient receiving process not only prevents discrepancies but also lays a solid foundation for subsequent warehouse activities.
How to Improve Receiving:
Prioritise labour management
Efficiency in the receiving process is crucial, and this starts with effective labour management. Software solutions that optimise workforce scheduling and task assignments can help allocate resources where they’re needed most, ensuring smooth operations even during peak times.
Even more importantly, invest in comprehensive training programs that cover every aspect of the receiving process. Make this training a core part of onboarding to ensure all employees are fully prepared before they start. Continuous training will keep your team informed about new technologies and best practices, ensuring ongoing improvement and operational excellence.
Embrace technology
Just as most other industries have experienced a technological revolution over the past decade, there has been a digital transformation in logistics.
Leverage technology to enhance the efficiency and accuracy of your receiving process. Implementing tools like barcode scanners and RFID systems can benefit inventory management by automating product identification and tracking. These technologies ensure that received items are accurately logged and placed in the correct storage locations, reducing errors and improving overall efficiency.
Additionally, warehouse management systems (WMS) can provide real-time data, helping you make informed decisions and optimise your receiving operations. By embracing these technological advancements, you can significantly boost productivity and maintain accurate inventory records.
Optimise your space
Effective space utilisation is key to enhancing your receiving process. Start with precise warehouse space planning to ensure every square foot is used efficiently. A well-organised receiving area reduces congestion and simplifies the flow of goods, making it easier for staff to process incoming shipments quickly and accurately.
Invest in adjustable shelving, modular storage units, and clear signage to create a flexible and organised space.
Regularly review and adjust your layout to accommodate changes in inventory and workflow, ensuring your warehouse remains optimised for peak performance.
2. Put-Away
The put-away process is crucial for transferring products from the receiving dock to their designated storage locations within the warehouse. Efficient put-away ensures that each product is placed in an optimal position, significantly impacting the safety, travel time, and retrieval of goods.
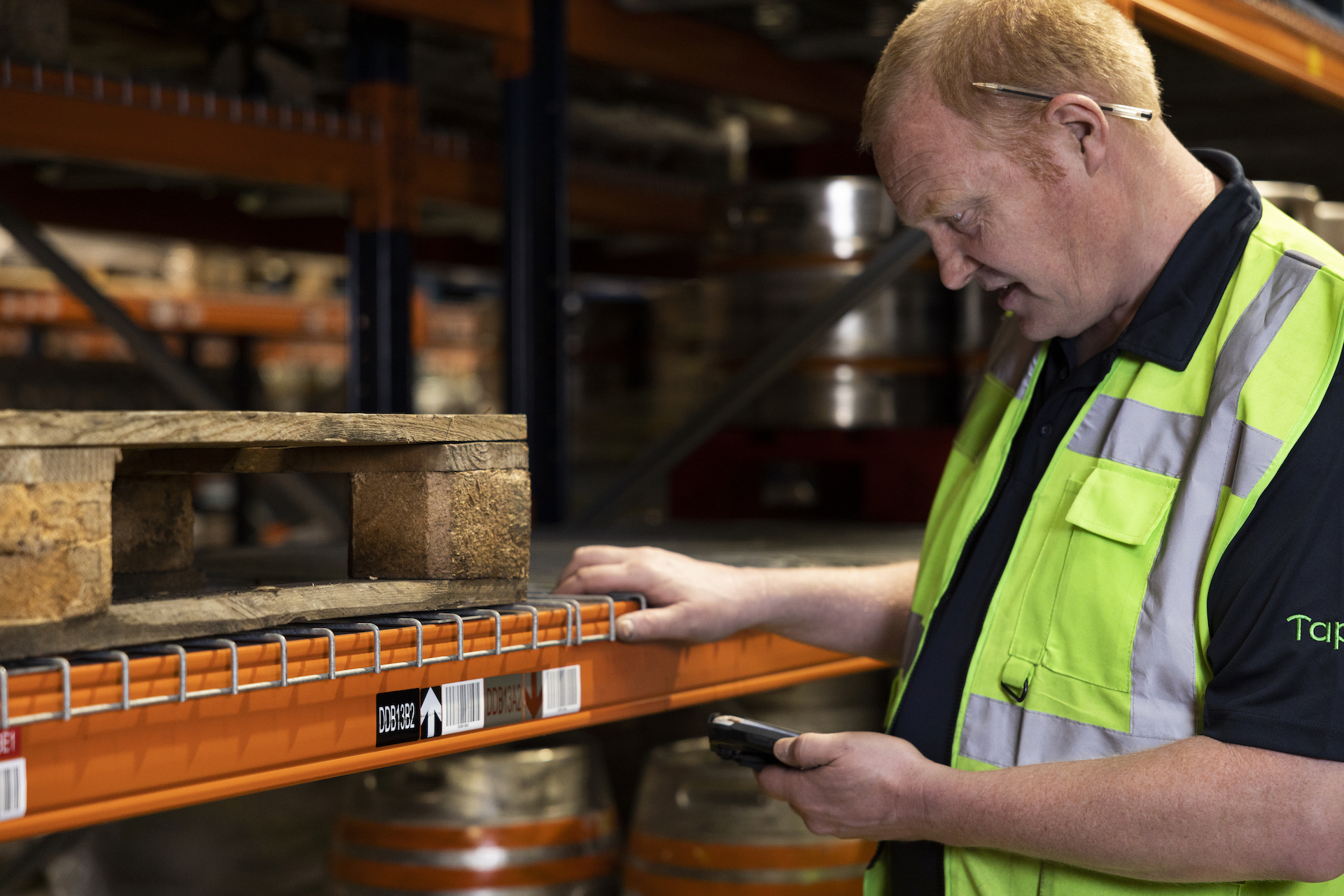
By strategically organising your warehouse layout, you can streamline this process, reduce handling times, and improve overall workflow.
A well-executed put-away system not only enhances operational efficiency but also sets the stage for smooth subsequent processes, such as picking and shipping.
How to Improve Put-Away:
Embrace smart warehousing
Enhance your put-away process by incorporating smart warehousing practices. For smaller businesses, start with affordable technologies like barcode scanning and mobile warehouse management systems (WMS) to ensure accurate product placement and efficient use of space.
For medium-sized operations, consider scalable automated storage and retrieval systems (ASRS), as the cost of these technologies has decreased, making them more accessible.
By leveraging these smart solutions, you can reduce human error, streamline operations, and maximise your storage capacity, all while keeping costs manageable.
Improve your warehouse slotting
One of the key principles of effective warehouse design is slotting. Warehouse slotting involves finding the best storage spots for each product.
By strategically placing items based on factors like demand, size, and weight, you can cut down on travel time and make picking more efficient. Proper slotting means less unnecessary movement, saving time and reducing labour costs.
Take the time to analyse your inventory and set up an optimal slotting system. Get this right, and you'll save money and avoid a few unnecessary headaches along the way.
Introduce real-time data tracking
Using real-time data is one of the best ways to boost your put-away process. Equip your team with up-to-date information on product demand, storage availability, demand forecasting, and more. Knowing details like product weight, delivery times, item type, and product size helps in making smarter decisions about where to store items.
Without real-time feedback, finding and using the most efficient warehouse layout becomes a guessing game. Implementing data tracking tools ensures that everyone has the information they need to keep things running smoothly and efficiently.
3. Storage
Storage is all about keeping your goods safe, organised, and ready for when you need them. It’s not just about stacking boxes – it's a systematic process that ensures everything is in the right place and in good condition.
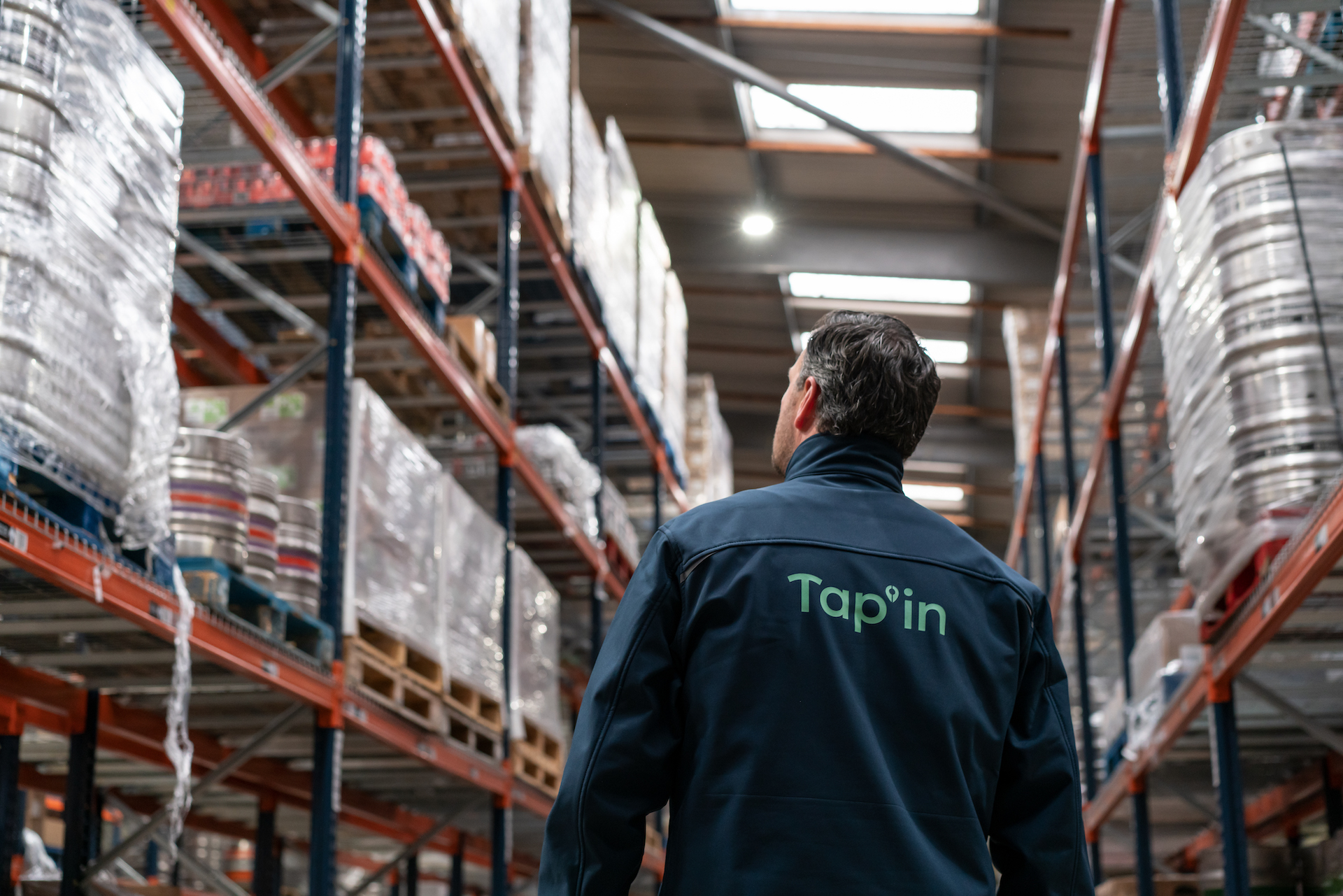
Effective storage keeps your products safe and organised, making it easy to find and access them quickly. It means you can manage your inventory better and keep things running smoothly. Good storage practices help maintain the quality of your goods, make the best use of your space, and cut down on costs.
How to Improve Storage:
Make the most of your space
Design your warehouse layout to boost space utilisation and reduce unnecessary movement. Use vertical storage with taller units and the right material handling equipment. Consider mobile shelving systems that can be adjusted as your needs change, reducing wasted space and boosting storage capacity.
The right warehouse layout not only uses every inch of available space but also improves workflow, making it easier for your team to locate and access items quickly. Think of creative solutions like stackable bins or mezzanine floors to further enhance your storage efficiency.
Keep track with the right tech
As mentioned already, use a Warehouse Management System (WMS) to keep a real-time eye on your inventory. As well as aiding other processes, when it comes to storage, a WMS will help ensure accurate stock monitoring, reduce errors, and speed up order fulfilment.
A decent WMS can also suggest the best storage spots based on item size, weight and how often they’re accessed.
By using tech to track inventory, you can make smarter decisions, reduce the risk of stockouts or overstocking, and keep your operations running smoothly. Plus, having this data at your fingertips means you can quickly respond to changes in demand.
Stay flexible and review regularly
Continuously evaluate your storage practices and adapt them as your inventory and business needs evolve. Regular reviews can uncover inefficiencies and highlight areas for improvement.
Try Reconfiguring layouts or upgrading storage solutions to better fit your current and future inventory. Stay flexible and open to change – what worked last year might not be the best solution now.
By keeping your storage strategies up-to-date, you can ensure your warehouse stays efficient and ready to meet new challenges. Regularly soliciting feedback from your team can also provide valuable insights for improvements.
4. Picking
The next crucial step in your warehouse workflow is picking, where stored products are collected and prepared for shipment. Order picking can be the most expensive part of warehouse operations, accounting for up to 55% of a distribution centre’s overall costs.
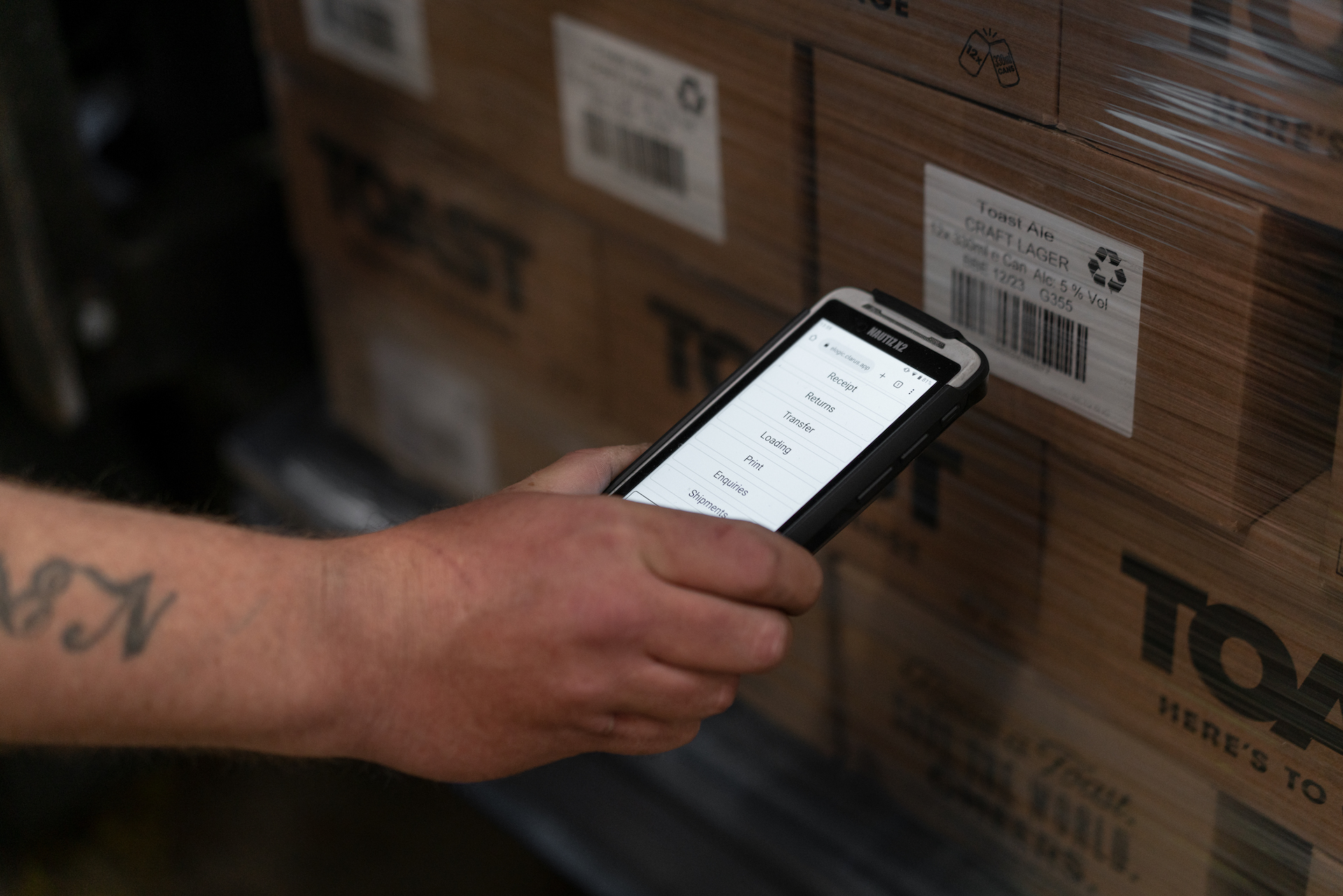
It’s essential to implement effective picking strategies to reduce complexity and higher costs. By optimising your picking process, you can improve labour efficiency and reduce expenses, as well as ensuring that orders are fulfilled accurately and promptly.
In short, efficient picking not only saves money but also boosts overall productivity, making it a vital component of your warehouse operations.
How to Improve Picking:
Choose the right warehouse picking strategies
The right picking strategy can have a big impact on overall warehouse performance. While many operations rely on the basic pick-to-order approach, exploring more tailored strategies can significantly boost efficiency. Some options include:
- Cluster picking: This method allows pickers to select and transport multiple orders at once, reducing travel time and increasing efficiency. Ideal for smaller items and high order volumes.
- Zone picking: In this approach, the warehouse is divided into zones, with pickers assigned to specific areas. Zone picking breaks up the process, reducing congestion and allowing pickers to familiarise themselves with their area, which can result in easier, more efficient management, especially in larger warehouses.
- Wave picking: Perhaps the most advanced method, wave picking groups orders at specific times and from specific zones. This strategy aligns picking with shipping schedules, replenishment cycles and staffing availability to maximise efficiency.
Each strategy has its advantages, and the best choice often depends on your product type, order volume and warehouse size/layout. Your WMS can also influence your options, so make sure to opt for a system that can support your chosen approach.
If you're unsure which strategy to adopt, you may be able to use warehouse simulation tools to identify the best fit for your operations.
Elevate your inventory control
One of the most effective ways to improve your picking process is to increase your warehouse inventory accuracy.
To increase inventory accuracy, you need to make sure your warehouse is well organised. Clear, consistent labelling makes it easier for pickers to locate items quickly and accurately. Additionally, consider investing in warehouse technology solutions like barcode scanners, RFID systems, integrating these with a robust Warehouse Management System (WMS).
Together, the right tools will help keep track of inventory in real-time, reducing errors and ensuring that stock levels are always up-to-date.
By improving inventory control, you can streamline your picking process, save time, and increase overall efficiency.
Limit and control access to inventory
Limiting and controlling access to your inventory is key to reducing the risk of products being misplaced or going missing. Implement strict access controls to ensure that only authorised personnel can handle inventory. This includes using secure entry points, employee badges, and surveillance systems.
Alongside these measures, enforce robust warehouse safety practices to protect both your products and your staff. Clear guidelines and protocols help maintain order and prevent accidents, ensuring a safe and efficient working environment for everyone.
5. Packing
Once you have your products to hand, packing is the process of collating products into their separate orders and preparing them for shipment. The main goals are to prevent damage during transit, keep packaging costs down and get all this done quickly and accurately.
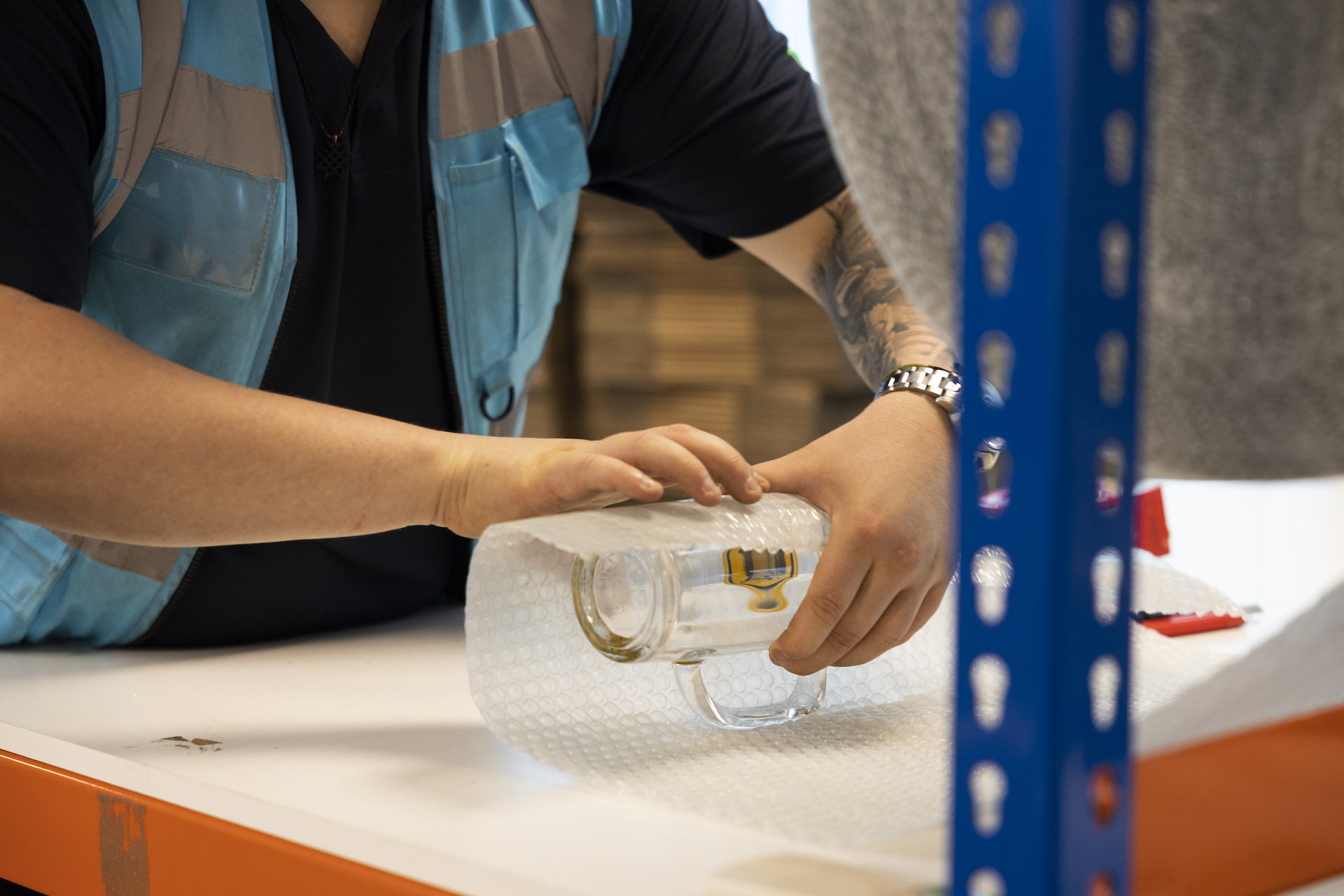
In today’s world, there's also a strong focus on sustainability. It's important to consider the environmental impact of your packaging choices. Opt for materials that are both protective and eco-friendly to reduce waste and delight customers.
How to Improve Packing:
Upgrade your packaging tools
If you have the budget, packing automation can bring massive benefits. Automation ranges from simple conveyor belts to sophisticated robotic systems that handle packing materials, fill boxes, and seal them without human intervention.
For smaller businesses, full-scale automation may be unrealistic. However, simple upgrades can still significantly enhance packing efficiency. Equipment such as semi-automatic tape dispensers, bag sealers, and box erectors can speed up the packing process without requiring a large upfront investment.
Standardise packing materials and procedures
Related to using the right tools, using standard materials (like boxes, padding and tape) and methods can lead to a much more efficient packing process. In addition, uniform box sizes and packaging materials can simplify training for new staff, accelerating the onboarding process and reducing packing errors.
Even better, standard processes will reduce variability in packing quality, resulting in a more consistent high-quality experience for customers.
Use packing software
Packing or cartonisation software can make a big difference in how efficiently you prepare orders. These systems help you choose the best materials and methods based on the items you're shipping – whether they’re fragile, bulky or a mix of both. The software can suggest space-saving packing configurations and calculate the best use of materials, cutting down on waste.
Plus, packing software (or modules within your WMS) can automate a lot of the paperwork, like creating packing lists and labels, removing some of the friction and improving accuracy.
6. Shipping
Shipping is the process where warehouse involvement ends and the journey of the goods to your customers begins.
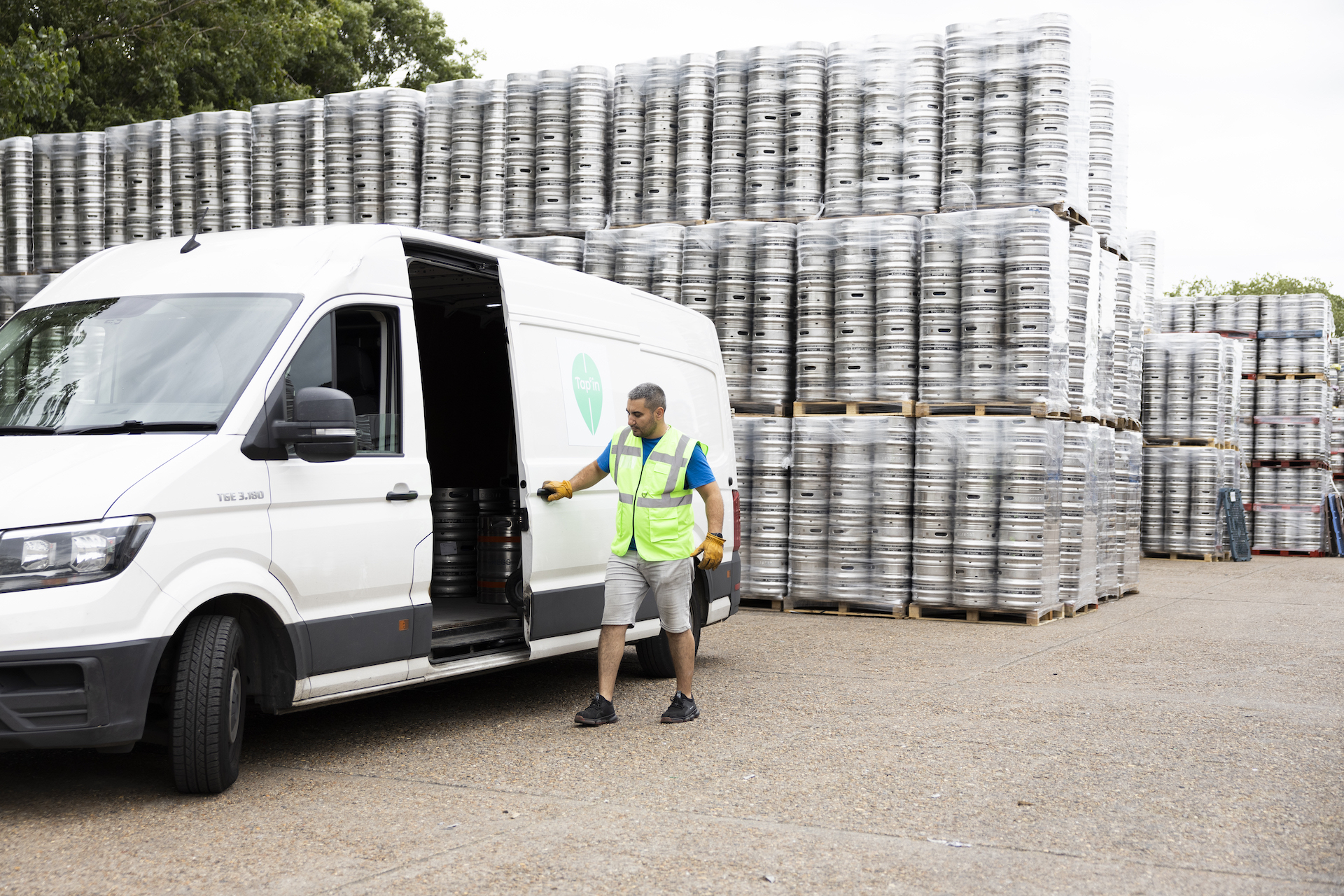
It’s a big part of the logistics process and entails locating and loading the correct orders, dispatching them to the correct customer, and delivering them on time and in good condition.
Just as the processes preceding shipping directly impact its success, the efficiency of the shipping process itself affects the success of the entire logistics operation.
How to Improve Shipping:
Prioritise correct documentation
Getting the paperwork right is crucial for smooth shipping. Every shipment needs key documents like shipping labels, bills of lading, certificates of origin, or shipping licences. These documents contain important details about the cargo and its destination.
The easiest way to keep things organised, especially at a large scale, is to leave this to your technology wherever possible. Spend some time upfront to develop a deep understanding of the documentation common to your business. Once you have a strong grasp of the requirements, configure your tools to take care of as much of this as possible.
Automation, backed up by adequate training for packing staff to spot issues, is the best way to ensure correct documentation and reduce the risk of delays or errors in shipping.
Create a loading strategy
A smart loading strategy can transform the often chaotic shipping process into a well-organised system. Start by setting up separate docks for shipping and receiving, which can prevent obstructions across unrelated activities.
If your warehouse handles a lot of goods, think about scheduling multiple shipments throughout the day, separate from receiving times. This can help avoid bottlenecks and keep things moving smoothly.
You can also consider using radio-frequency identification (RFID) technology. RFID tags store all the information related to a shipment and send it to a central database. For some types of goods, this makes it easier to organise and monitor shipments compared to manual methods. With RFID, you can track everything in real-time, improving shipping visibility and reducing errors.
Maintain the shipping docks
It’s a simple tip, but cluttered or disorganised shipping docks can quickly get in the way and lead to errors and delays.
Whether you have multiple dock doors and sophisticated loading equipment or a more modest setup, taking good care of your shipping areas will keep both receiving and shipping running smoother.
As a bonus, tidy and organised shipping areas can help improve warehouse security and the safety of your employees.
7. Returns Management
Returns management, also known as reverse logistics, is a key part of the supply chain that goes beyond just accepting returned items. It's about understanding why returns happen, handling them efficiently to recover as much value as possible, and using what you learn to improve the overall customer experience.
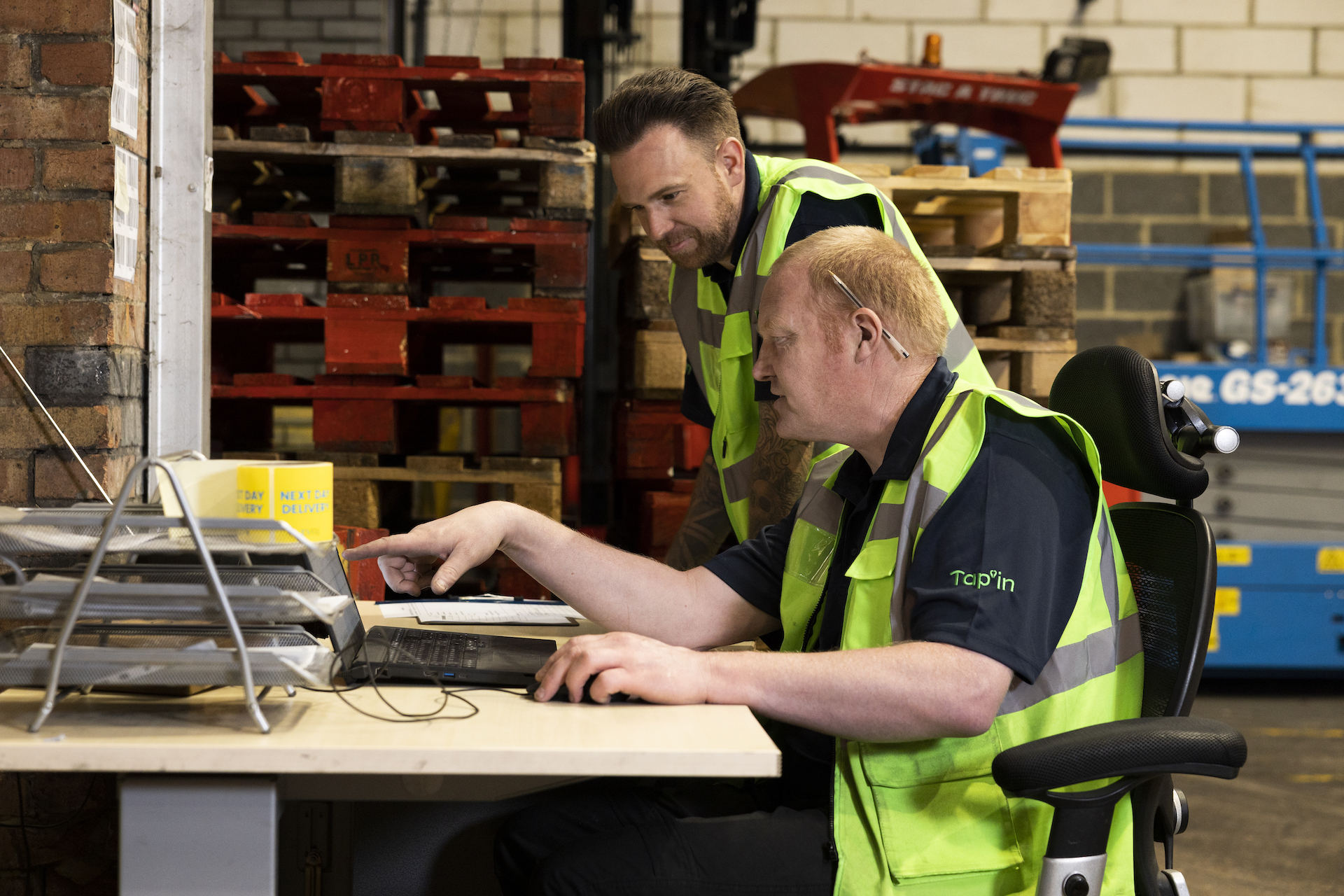
Done right, an effective returns management process will boost customer satisfaction, improve product lifecycle management, and positively impact your bottom line.
Here are some ideas to improve your returns process and turn the challenge of returns into an opportunity for better warehouse management and customer engagement.
How to Improve Returns:
Try workflow automation tools
Advanced software can help you manage your returns by using data and predictive analytics to forecast your returns volume and automate the returns process.
Warehouse automation and other warehouse reporting tools that interrogate the reasons for returns and relay customer feedback to the company can help reduce returns in the future.
Monitor the cost of returns
It's important to track the cost of handling returns as part of your overall warehouse cost analysis. Returns can be a significant expense, but also an area that offers considerable opportunities for savings and improved customer experiences.
For example, if the cost of returns is high, look for creative ways to revamp the process. For instance, if a product can’t be resold, you might offer a refund without requiring the item to be sent back. This approach can save both time and money, all while keeping your customers happy.
Stand on the shoulders of giants
Major online retailers, like Amazon, have leveraged their scale to master the art of returns management. Observe their processes and steal or adapt what you can.
For example, Amazon has implemented many clever and creative strategies in its returns management processes that not only reduce costs but massively improve the customer experience. Can you think of ways to adapt any of these strategies?
- Centralised returns centres: Amazon operates specialised returns centres dedicated to processing returned items. Centralisation allows for quicker sorting, assessing, and reintegration of products into inventory or alternative channels.
- Automated sorting systems: Amazon automatically sort returns based on their condition and final destination (e.g. restocking, recycling, liquidation), reducing manual handling and speeding up processing. Smaller businesses could explore smaller scale automation or semi-automated options to improve sorting efficiency.
- No-box and no-label returns: Amazon allows customers to return items without a box or label at Amazon stores and some partner locations. This simplifies the returns process for customers and reduces packaging waste. Small businesses could partner with local stores or provide simple drop-off points to facilitate easier returns.
- AI-powered decision making: Leveraging artificial intelligence to decide the best course of action for a returned item (whether to refurbish, resell, recycle, or dispose) can cut costs associated with handling returns. Smaller enterprises can use simpler decision-making software tools that help determine the most cost-effective action for returns.
- Pre-emptive refunds and keeping the product: In some cases, Amazon issues a refund and lets customers keep the product if the cost of processing the return exceeds the item’s value. Small businesses can adopt this approach selectively, particularly for low-cost items where return processing would cost more than a refund.
- Data analytics to reduce returns: Amazon uses data analytics to understand why items are returned and to fix underlying issues. This could involve improving product descriptions, adjusting packaging, or changing shipping methods. Small businesses should regularly analyse return reasons and adapt practices to reduce future returns.
- Resale of returned goods: Through Amazon Warehouse, Amazon sells returned goods at a discount, managing to recoup some value from items that cannot be sold as new. Similarly, smaller businesses can consider setting up a dedicated section on their website for discounted, open-box items.
- Packaging innovations: Amazon invests in packaging research to develop materials and designs that reduce damage during transit, thereby lowering return rates. Smaller companies can also focus on improving their packaging practices to reduce damage and subsequent returns.
These strategies are scalable and can be adapted to varying degrees depending on the size and capability of your business. In logistics, it often pays to monitor the strategies of the biggest names in the industry.
8. Reporting
The final stage of the warehouse logistics process is reporting. This aspect involves collating and analysing data from throughout your logistics operation to learn about and improve your workflow.
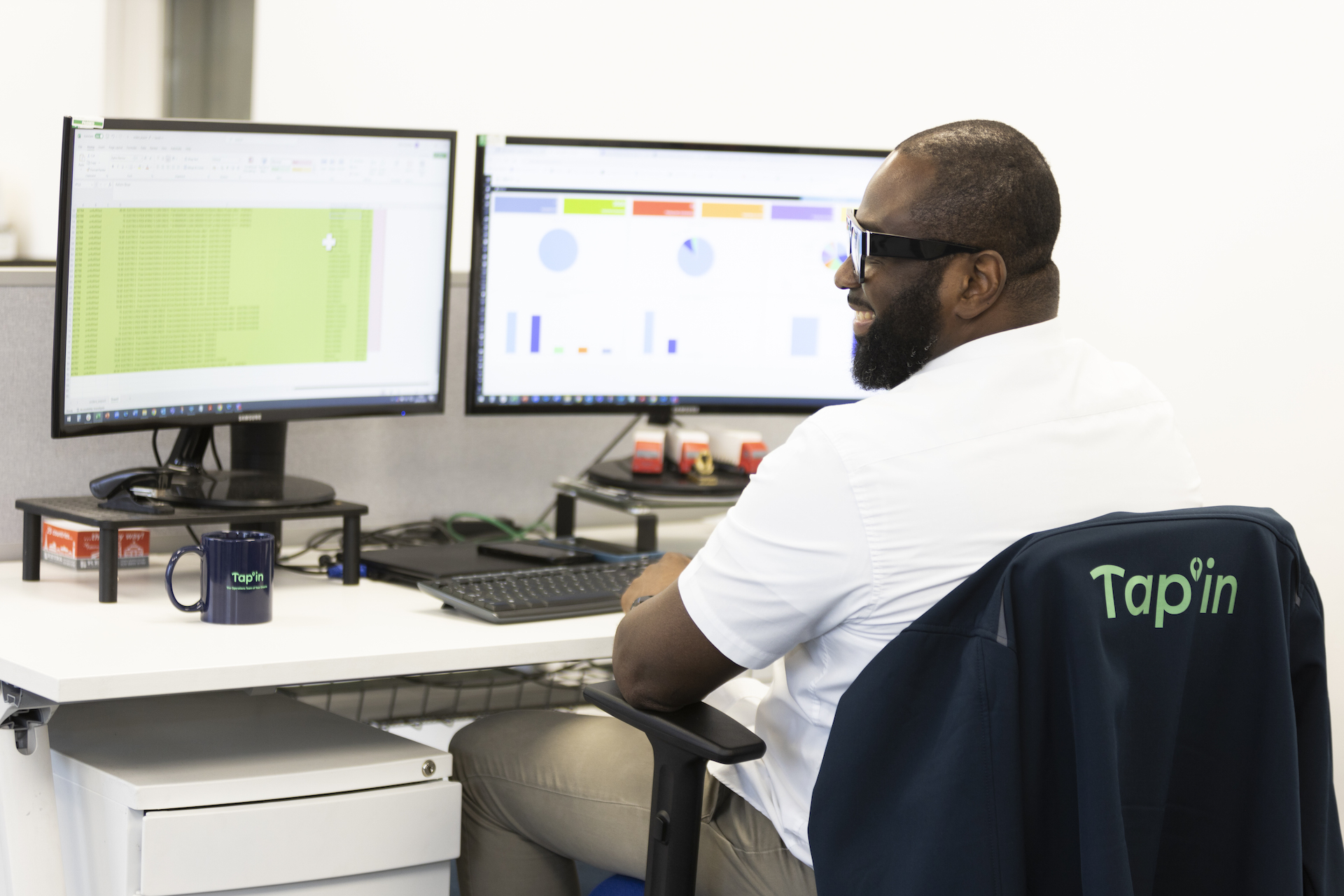
The benefits of effective logistics reporting include increased regulatory compliance, enhanced risk management, improved sustainability and optimised order fulfilment.
How to Improve Reporting:
Integrate the Internet of Things
The Internet of Things (IoT) is transforming logistics, and it can work wonders for your warehouse reporting. By integrating IoT, you create a network of smart devices that enhance reporting and bring your supply chain into the modern age.
IoT applications come in various forms, such as geolocation management tools, inventory tracking systems or even automated guided vehicles. These technologies help you collect real-time data, making it easier to track inventory, monitor equipment, and manage operations efficiently.
With IoT, you get a clear, up-to-date view of your entire supply chain, allowing for smarter decisions and smoother processes.
Define your performance objectives
Before you can understand the success of your logistics operation, you need to determine which aspects you want to report on and how you’ll measure success.
Many logistics operations monitor metrics such as delivery time, fulfilment accuracy, product quality and customer satisfaction. Whatever you choose, make sure to keep your end goals in mind - a strong north star metric must be derived from a true understanding of what action provides real value to your customers.
Once you have the right metrics in place, you can use warehouse benchmarking to compare your performance against industry standards. This comparison will help you understand where you stand and identify areas for improvement.
By setting clear goals and regularly reviewing these metrics, you can continuously enhance your operations and stay ahead of the competition.
Review your operations regularly
And on that note, if we’ve said it once we’ve said it a thousand times, you need to review your metrics and processes regularly - make it a habit.
You can do this by conducting regular audits, holding internal evaluations and assessing your objectives continuously. It also helps to maintain great relationships with all levels of your warehouse staff, as their opinions are an invaluable resource in identifying underlying issues.
Implementing iterative methods like Six Sigma can be particularly effective in warehousing. Formal approaches help you analyse your entire logistics process in detail, identifying inefficiencies and areas for improvement.
Is Your Warehouse Holding You Back? Leave the Warehouse Optimisation to Us!
Managing a warehouse can be overwhelming, with countless elements needing to work together seamlessly. Instead of juggling all these processes yourself, why not let the experts handle it?
At Tap’in, we specialise in hassle-free warehousing and logistics. Our team uses advanced techniques to ensure your orders are fulfilled accurately and efficiently, giving you more time to focus on growing your business.
We understand that trusting a third party with your operations is a big step, but with Tap’in, you're in good hands. Our personal approach and direct communication mean you can be as involved as you want, while we take care of the rest.
Ready to take your operations to the next level and watch your business grow? Get in touch with our friendly team today to discover how our 3PL services can transform your business.
You’re one step away from finding the operations team of your dreams.
Get in touch today.
Fill in the form below or e-mail us on sales@tapin3pl.com